Discover how wienerberger partnered with Heatcatcher to implement this vital energy-saving project at its Broomfleet site.
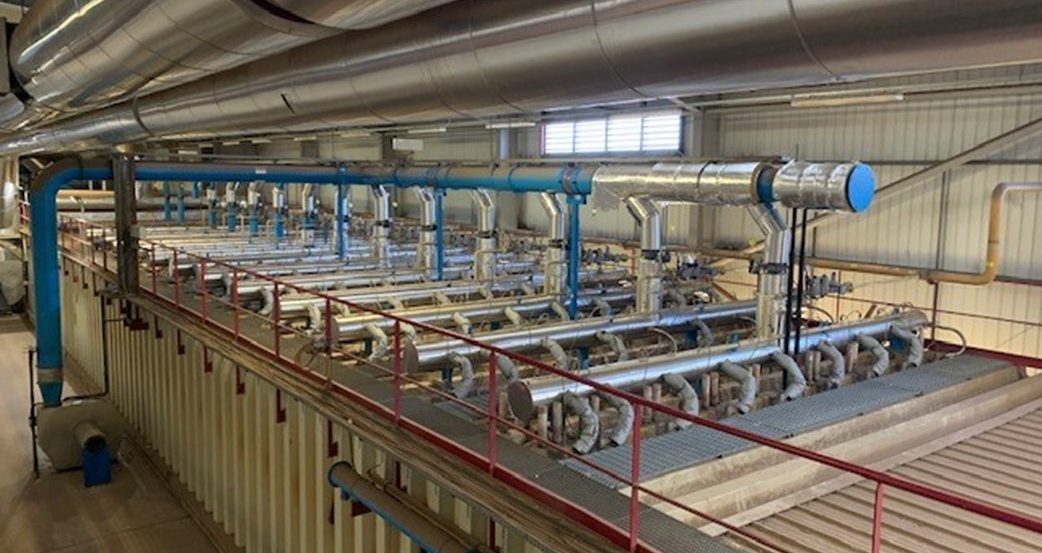
Discover how wienerberger partnered with Heatcatcher to implement this vital energy-saving project at its Broomfleet site.
wienerberger’s Broomfleet tileworks in East Yorkshire manufactures clay roof tiles using gas-fired tunnel kilns and dryers. While previous projects had focused on optimising the energy efficiency of the firing process, there was still opportunity to reduce energy demand further by recovering waste heat from the kiln exhaust system in Broomfleet’s production line named Factory 4.
The new system recovers waste heat from the tunnel kiln exhaust gas and reuses it to preheat the combustion air and drying chamber air. We partnered with Heatcatcher, experts in implementing systems to recover waste heat and power, to implement this vital energy saving project.
The installation of this new heat recovery system was supported by funding from the UK Government department for Business, Energy & Industrial Strategy (BEIS) through the Industrial Heat Recovery Support (IHRS) programme.
“Working alongside Heatcatcher, wienerberger made the transition a smooth process from concept to a completed installation, with the support and expert knowledge at all stages,” said Steve Marshall, Thermal Process Engineer (North) at wienerberger UK & Ireland. “This included the IHRS application, detailed engineering report to ensure correct specification of the equipment, and finally the full project management of the installation and commissioning of the equipment.”
“The system design is first of its kind for the ceramic industry, indirectly transferring heat between heat exchanger locations with a pressurised hot water circuit, instead of the direct ducted method over long distances,” said Darren Bryant, Heatcatcher CEO.
Since the improvements were completed in August 2022, Broomfleet Factory 4’s production process is saving around 525 MWh of gas a month. That equates to a reduction of over 700 tonnes per year of carbon dioxide emissions (tCO2e).
“This project has demonstrated the benefit of installing heat exchangers on factories with excessive exhaust temperatures to recover the wasted energy for deployment back in the process,” said Tim Dudding, Plant Manager at wienerberger Broomfleet. “This represents a significant step to achieving the ambitious carbon reduction targets Wienerberger has set across the business.”
This project compliments our transformational investment to install an electric kiln at wienerberger’s Broomfleet site, which will make it Europe’s first clay roof tile plant to eliminate the use of natural gas (and the associated CO2 emissions) from the drying and firing processes, reducing the carbon emissions from these production lines by 75 per cent. These revolutionary plans are a vital steppingstone to achieve wienerberger’s commitment to reduce carbon emissions by 40% by 2030, compared to 2020 (kgCO2e/quantity of products ready for sale).