wienerberger has a responsibility to ensure that natural resources are available for future generations. Explore the key stages of our production process and how we manage resources, from quarry to lorry – and beyond.
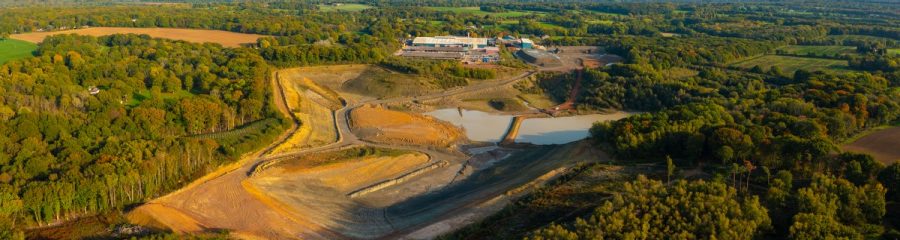.jpg)
wienerberger has a responsibility to ensure that natural resources are available for future generations. Explore the key stages of our production process and how we manage resources, from quarry to lorry – and beyond.
At wienerberger, we understand that for our business to thrive, we need to create enduring value – for us and for those around us. As well as providing products and services that respond to the global challenges of climate change, biodiversity loss and resource scarcity in the built environment, Wienerberger must become a net-zero emission, nature-positive business.
The transition to a net-zero economy requires careful planning, incorporating known technological innovations and encouraging creativity. Our Sustainability Roadmap outlines our ambitions for 2030 and steps towards these goals. Here we take a look at our production process in more detail, and how we’re already paving the way for a production system that uses fewer resources.
The most important raw material for our ceramic products, such as bricks, pavers and roof tiles, is clay. Most of our factories have a dedicated quarry in close proximity to the factory, minimising transport distances for clay to the production site. This also means wienerberger has good oversight of the environmental and social practices for the majority of our material supply chain.
The remaining raw materials are brought into our manufacturing sites and we endeavour to use quality local suppliers to minimise carbon dioxide emissions and other transport impacts. In 2022-23, the average milage per tonne of raw material delivered was 0.7 miles for brick products, and 9.0 miles for roof tile products.
Our factories pursue zero clay waste in production by returning off-cuts from the shaping process and imperfect unfired products to the clay stockpile. This clay is then reused in future production runs.
Where fired ceramic products are deemed not to have met our high quality standards, these can be crushed and recycled either in the manufacturing process, or sold on as aggregate.
wienerberger’s inclusion of materials from alternative, recycled, and secondary sources (MARSS) reduces the consumption of virgin clay resources and, by utilising by-products from other industries, wienerberger diverts material from landfill. The percentage of MARSS used varies by factory and by product, so please request current MARSS percentage content when ordering.
In addition, wienerberger has embraced the challenge to ‘do more with less’ by investing in research and development to make our products strong, light and efficient. That means that less clay and raw materials are required to create a high performance product.
Water is an essential ingredient for manufacturing bricks, clay roof tiles and pavers – water is what gives unfired clay its unique plasticity, perfect for shaping. So, we believe that it’s essential that we use water responsibly.
Some of our factories reduce their total water consumption by directly reusing water for washing product moulds or by recycling water for use in other applications such as HGV wheel washing.
We have partnered with water experts from both consultancies and universities to identify opportunities to save water and reduce our water footprint. This has led to a better understanding of water quality thresholds which in turn has enabled us to replace mains water (drinking quality) with water from non-mains sources such as rainwater harvesting and our onsite lagoons. These innovations increase our resilience to water supply shortages.
Once clay bricks, roof tiles and pavers are shaped, they must undergo a drying process before being fired in a kiln. Dryers and firing kilns are typically gas-fired. In order for clay to offer the durability, strength and fire resistance required, it must be fired at very high temperatures – in the range of 1000 to 1100 degrees Celsius.
The carbon dioxide emissions generated from energy consumption in the brick and roof tile manufacturing process can be divided into two categories: direct emissions from combustion (the burning of gas and oils) and indirect emissions related to electricity generation. However, a third source of carbon dioxide emissions exists, called process emissions, which are released from clay during firing.
wienerberger’s Broomfleet tileworks was able to optimise the energy efficiency of the drying and firing process by recovering waste heat from tunnel kiln exhaust gas and using it to preheat the combustion air and drying chamber air. The heat recovery improvements will save over 700 tonnes per year of carbon dioxide emissions (tCO2e). Read more about this heat recovery project.
Collaborative investigations with British Steel have also allowed wienerberger to explore further waste heat recirculation practices. Specifically, this could involve reusing heat from cooling systems to pre-heat the combustion air in brick kilns. Applying this technique to brick kilns could reduce the amount of gas used in the process, and in turn the carbon emissions from wienerberger’s operations.
During this project, British Steel and wienerberger also exchanged perspectives on how the firing equipment currently in-use could be adapted to successfully introduce hydrogen to the fuel mix. This is important as plans to inject hydrogen into the gas transmission and distribution networks are outlined in the UK Government’s Net Zero Strategy and will help to reduce the carbon content of gas consumed the Foundation Industries including steel and ceramic manufacturers. Read more about our investigations into combustion efficiency.
wienerberger has committed to reducing plastic packaging by 30% by 2023, compared to 2019 levels. wienerberger’s procurement, operations and H&S teams are collaborating with our customers and logistics partners to trial alternative packaging solutions.
While we test new packaging configurations, wienerberger has made the decision to remove the coloured ink from our plastic packaging. Removing coloured ink means the plastic packaging can be recycled as a higher-grade material, thereby helping to avoid plastic disposal via landfill/incineration and ultimately reducing our reliance on virgin raw materials. Read more about how we’re reducing plastic packaging.
In addition, the majority of wienerberger bricks and pavers are stacked in a pattern that allows transportation by forklifts without use of a pallet. Wooden pallets are generally only used for transporting special shaped bricks and roof tiles, after which the pallets can be returned to our concrete roof tile sites for recycling.
With factories located in the south, midlands and north of England, transport distances between production and construction sites can be kept to a minimum, further reducing the environmental impact of our operations.
Through our continuous dematerialisation efforts, we have reduced the weight of bricks, and this created an opportunity to review brick pack weights and the pack configurations. We were able to ensure optimum load capacity while keeping maximum focus on the safety of the packs on each load, and the health and safety of delivery drivers and operatives. Our load optimisation efforts will reduce the total number of loads by 1,234 and over 182,000 delivery kilometres, equivalent to over 4 and a half times around the earth’s equator. Read more about load optimisation.
Where possible wienerberger’s contracted road hauliers have an ISO 14001 certified Environmental Management System and use trucks fitted with technology to minimise noise and reduce emissions to Euro 6 standard. To minimise the environmental impact of transporting our products a full load delivery price incentive is used. If this is not possible, we aim to group orders to achieve a full load delivery. When importing products from Europe we charter vessels that carry around 850,000 bricks per load, attaining lower emissions per mile than the equivalent road transport.
By designing for durability and material efficiency at the outset, wienerberger avoids creating waste at our factories. If a fired product does not meet our strict quality tests, it will be separated and recycled. Common recycling routes include crushing for aggregate or recycling back into our manufacturing process.
Nearly all the waste resulting from the manufacture of clay construction products is non-hazardous. Very small quantities of hazardous waste are sent to specialist contractors with some, such as oily rags and electronics, being recycled for further use. For non-hazardous materials, wienerberger achieves high recycling rates. Where possible we return used materials and equipment to our suppliers for direct reuse or recycling.
We are transitioning our company car fleet to electric vehicles, supported with the installation of EV charging points across our factories and offices. Once implementation is complete, we expect this to reduce emissions from business travel by 500 tonnes of CO2e emissions per year, compared to 2019 levels. We anticipate that all company car users will order either a full Electric Vehicle (EV) or Plug-in Hybrid Electric Vehicle (PHEV) by the end of 2023. Read more about how we’re reducing business travel emissions.
When quarries reach their end of life they are typically restored to natural habitats where wildlife can flourish. Our operations of quarrying and manufacturing have created a variety of habitats which, when combined with the land that we own and manage, provides for a biodiverse landscape. Even industrial buildings and active quarries are home to wildlife such as nesting birds, insects and wildflowers.
Many wienerberger sites have areas listed as nationally important Sites of Special Scientific Interest (SSSI) or local designations for ecological or geological significance. These sites are managed to maintain and promote biodiversity in conjunction with Natural England and relevant local authorities. Our management techniques include hedgerow planting, coppicing on rotation and mowing to maintain wildflowers and herbs which in turn support a variety of insects and small mammals.